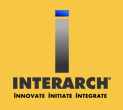
Interarch in 2014 designed, manufactured and delivered a fabrication shop and assembly shop for JCB India Limitied in Jaipur.The buildings are spread over the area of 30400 Sq. Mt and 22800 Sq. Mt. respectively.
The project is designed according to the latest IS design codes, IS 800: working stress design for both the buildings with consideration given to all the geographical data like wind velocity, seismic zone as per IS standard for every particular site. The lateral forces resulting from the seismic or wind loads are resisted by diagonal bracing and jack portals at intermediate column locations. The design of the building was such that temperature was kept in control for monitoring the thermal expansion and contraction.
The expertise of Interarch design department reduced the engineering time of the fabrication shop and assembly shop which was very complex and new innovation has been done to design the building.Interarch for the first time designed a building bearing heavy load of approximately 225 M hanging from the roof and for the column grid of 40 x 24 M. Higher grade of 450 MPa steel has been used for the built up members.
Interarch had to deploy innovative solutions like highest safety standard which were followed in line with the international standard to achieve zero accident, Logistic and warehousing control at site to meet site standard norms. Daily tool box meeting to review the site status and way forward was done, regular Quality check jointly with client was done & corrective measures to achieve best quality in line with global standard were taken. Highest level of safety standard was showcased by Interarch Project Management team at the site achieving zero accident with over 150 skilled workers working at site.
The project was completed in record period of 6 Months.
JCB India Limited, Ballabgarh (Haryana), India’s largest manufacturer of construction equipment is a fully owned subsidiary of JC Bamford Excavators Limited, UK. The company offers 24 different machines in seven product types such as Backhoe Loaders, Loading Shovels, Tracked Excavators, Compactors, Telehandlers, Skid Steer Loaders and Pick and Carry Crane.
Project Name | JCB India Limited - Fabrication Shop |
---|---|
Project Location | Rajasthan |
Area | 30400 Sq. M |
Features | Fabrication Shop
|
Project Name | JCB India Limited - Assembly Shop |
---|---|
Project Location | Rajasthan |
Area | 22800 MT |
Features | Assembly Shop
|
Interarch designed, engineered, and delivered the first Guar Gum building in Pre-Engineered Building technology in India. Interarch was awarded the project for executing new manufacturing facility for Sunita Hydrocolloids Pvt. Ltd. at Jodhpur, Rajasthan using its expertise in complex engineering and innovative design solutions.
Pre-Engineered Building technology was not used for such an application in the recent past, customer preferred only RCC Buildings due to the complexity of the buildings. For the first time Interarch bagged this project of constructing the Guar Gum Building using innovative design technology.
The building is utilized as a process plant for making Guar Gum powder. There are 6 different units or towers in this project. Each tower has 3 levels of floor with deck panel and floor opening for equipment pipelines.
Total height of each tower is 15.3 M. The most important aspect of this project is, all the towers will be covered by a single shed of 33M clear span and a clear height of 23M.
All towers are connected internally by walkway thereby giving it a one point access. Industrial louvers have also been installed for proper ventilation. Each wall has a Liner panel with insulation.
Each floor is designed considering the Static & Dynamic loading and without Cross Bracing and Mezzanine with Bi-directional force transmission with beam.
The project is designed according to the latest IS design codes with consideration given to all the geographical data like wind velocity, seismic zone as per IS standard for particular site.
Project Name | Sunita Hydrocolloids |
---|---|
Site Location | Jodhpur, Rajasthan |
Building Usages | Process plant for the production of Guar Gum Powder. |
Design Code | Latest IS design code IS 800:2007 |
Project Area | 2400 Sq. M |
Total Tonnage | 650 Ton |
Special Features |
|
The agriculture sector of India has over the years been the single most important component of the economy. In the past two decades a lot of emphasis has been given to the technological developments in the agricultural sector, in order to raise the standard of living and the quality of the produce of farmers. Over the years the sector has evolved using state of art technology and business models to make it commercially successful via public and private enterprises.
Two such examples of innovation in the rural agricultural sector are the much talked about ventures of ITC and DCM Shriram Consolidated Ltd. (DSCL) called Choupal Sagar & Haryaali Kisaan Bazaar respectively. Chaupal Sagar is a rural retail shop & warehouse with a size of 1500 – 2400 Sq m. Harayaali Kisaan Bazaar is a chain of centres across the rural landscape of the country aimed at triggering a qualitative improvement in Indian agriculture. Each centre is spread over 3 to 4 acres of land, in hinterland locations, offers to farmers.
Interarch Building Products Pvt Ltd has been instrumental in the creation of many rural retail projectsacross the country. Their knowledge of warehousing and rural retail and their precision in execution has been brought to the forefront through their exceptional work for Chaupal Sagar and Haryali Kisaan Bazaar.
Interarch played an integral role in bringing up the steel warehouse buildings of Choupal Sagar for ITC in a short span of time with 5 larger than life size buildings across the rural areas of the country; majority being in Uttar Pradesh&Madhya Pradesh. The warehouses were made using Interarch’s much spoken about roofing systems TRACDEK® Hi-Rib Bare galvalume with insulation, with cladding systems of TRACDEK® Hi-Rib SMP.
For Haryaali Kisaan Bazaar Interarch have used TRACDEK® Hi-Rib Bare Galvalume with insulation for the roofing’s while TRACDEK® Hi-Rib SMP Coated Galvalume have been used for cladding. Haryalli Kisaan Bazaar is a rural retail shop & warehouse with a size of 1500 – 2200 sqm. The DSCL venture is currently present in the states of Uttar Pradesh, Punjab, Madhya Pradesh, Haryana, Andhra Pradesh, Rajasthan and Maharashtra.
The success of Choupal Sagar has heralded a new era in the Indian agro-sector. This revolution led to seeding of the idea of raising more such replications in the other untapped areas.
The main reasons for the success of the platform have been the involvement of local farmers and maintenance of the rural IT network by the corporate entity.
Interarch has in its work with both companies, executed various modular systems and has done over 65 buildings in over 65 locations for DSCL Hariyali Kisaan Bazaar and 5 buildings in 5 locations for ITC.
Interarch specialized in setting up 2-3 types of modular buildings that were easily manufactured as per requirement of site within 1 week and shipped to site, assembled and finished in remote locations. Interarch's exceptional abilities in turnkey design, manufacture, supply and execution of such modular systems, enable it to provide fast and effective solutions to remote projects that require standardized, multiple, modular building execution.
The Indian PEB industry originally operates on a very stereotypical and common function, wherein the pre-engineered building supplier comes in at a stage when most of a project has been conceptualized and architectural details and elements have been fixed. The PEB supplier then custom designs the building based on the given requirements of the project, supplies the material and nominates a third party erector with a team of 30-40 people at max to complete the execution of the structure. A typical pre-engineered project in India caters to any simple shed for industrial or warehousing use.
What makes Interarch’s way of working in India different from the rest of its competition is one of the main reasons that explain the highlights of why the Interarch work at the IGI-Terminal 3 project stands apart.
Interarch is one of the leading “turnkey” pre-engineered steel construction solution providers in the country, which by literal definition means that Interarch is one of the only leading pre-engineered solution providers that has the in-house capability and knowhow to provide integrated conceptualizing, design, manufacturing, supply & logistics and, on-site project management and execution capabilities over its entire pan India operations.
Very few of Interarch’s competitors come close to being able to offer the turnkey functions and over-all project handling that Interarch offers the industry. Due to this, Interarch had even before the IGI-T3, executed project of greater and more complex magnitude on a turnkey basis.
Interarch was chosen amongst many international and Indian-JV bidders from an international bidding process, to come aboard under lead contractors Larsen & Tubro and GMR-DIAL, to execute the structural steel works for the Domestic and International Piers of the Delhi International Airport IGI –Terminal 3 project as well as the entire roofing system for the entire terminal building.
The IGI-Terminal 3 project would come to be known as one of the largest and most fast paced projects undertaken by any developer on Indian soil, to be built in time for the commonwealth games in New Delhi in 2010.
Through its course Interarch would design, manufacture and construct over 7500MT of steel in under 8 months and would design, procure and lay over 1.2 million square meters of roofing material to cover one of the largest buildings in Asia.
Interarch’s ability to provide complete turnkey solutions in pre-engineered steel construction and in-house handling of the entire EPC function of this project led it to become a critical player responsible for the entire Terminal 3 project.
When Interarch was invited to bid for the tender, it was only asked to consider responsibilities towards the 175,000 sq mt’s of 7-layer state-of-the-art roofing system that was required for the terminal building. While studying the project drawings during the bid for the tender, Interarch design and technical team realized that apart from the roofing for the PIER’s and the Passenger Terminal Building, the entire superstructure under the roofing system of the International and Domestic Piers at IGI-T3 were being visualized by the customer in steel and were ideal for a pre-engineered steel structural system, rather than the originally planned conventional site fabricated steel system.
Due to its years of experience in structural steel design, Interarch proposed to its customer the advantages of considering a pre-engineered structural steel system for the almost 3km’s of terminal Pier’s.
On advanced design and study under the expert guidance of Interarch design engineers, Interarch was able to offer a state-of-the-art design solution for the terminal building piers which would save the project and the customer over 30% in steel tonnage as well as cut the construction time by almost half.
On presentation and acceptance of its abilities customize and value add to the project in terms of engineering and a complete EPC solution, Interarch successfully managed to convert the project to a pre-engineered steel system to aid to the execution speed and the overall longevity of the project design.
Interarch, having an already nationwide presence with manufacturing units all over the country, went a step ahead in this project and offered one of its manufacturing units in Greater Noida to be dedicated to cater to the manufacture of the high-end steel for the fast paced requirements of the IGI –T3 project. Being located in a 50km radius to the project, Interarch’s Greater Noida facility took on the challenge to produce some of the largest and most complex, and utterly mindboggling pre-engineered structural steel systems for the Terminal 3 project.
Interarch’s project management and contracts division took over a 5 acre allotted yard space at the project site and built on location its’ offices, on-site handling, logistics and satellite manufacturing and finishing facility at the airport site itself.
To save time, Interarch manufactured all its sections in-house in Greater Noida and shipped them to site over night in lots. Close to over 300,000 parts and sections were shipped to site along with hardware for assembly during the course of the project and execution work.
Once the material reached the site, each part and piece of the giant airport terminal was carefully sorted and put in line for final painting and fire-proof coating which was undertaken by specialized painting teams and Interarch sub-contractors at the its site establishment at DIAL T3. Once painting was completed the parts were sorted with respect to part number and location as per grid and location tally spanning almost 3km’s of building construction and were transported upto 2km’s within the site, to the respective work fronts for assembly by simple bolt-on construction requiring no site welding and cutting and then lifted piece by piece to the top of the building to form the roof structure system.
By having everything under its belt from design, manufacture, supply, logistics and project handling – Interarch took over the responsibilities of the structural steel work and roofing works from lead contractor L&T, and under its overall PMC controlled the entire execution and feed to the project site from its supply chain.
The terminal 3 project was no meager feat and it required multiple handling of pre-engineered construction activities spread over an area of almost 5 square km’s and over almost 20 active work fronts on different parts of the building each with their own dedicated resources for power, construction equipment and manpower teams, all deployed by Interarch PMC. The Interarch project management team deployed more than 200 engineers at the site, including heavy construction equipment, and over 2000 skilled workmen to execute the project work successfully with safety and quality.
All site coordination was handled from its central control at the DIAL T-3 site office and wireless communication over local radio’s assisted construction and coordination of the entire project from material handling & feed to front, to lifting, assembly and final crane lifts to the building location and rooftop.
Interarch shifted an entire team of senior in-house design, manufacture, project management and construction experts to the DIAL site for a period of over 10 months to handle the structural steel execution as well as the roofing of the gigantic terminal building. By coordinating its outputs for an ever-changing airport site, which required constant pre-planning, planning and then further re-planning to cater to the dynamic site conditions, along with constant design and redesign requirements from the customer for interface details and adaptability and compatibility to various construction aspects, Interarch was able to give lightening fast response times and streamline its system dynamically to cater to the project from its design support set up’s directly at site.
The IGI-Terminal 3 building is the second largest integrated terminal building of its kind in Asia and its roof covers an area of more than 45 acres.
Once Interarch completed the structural steel design, in-house manufacturing and execution for the steel package of the project, it commenced operations on roofing.
Interarch operations were deployed after completion of its pre-engineered steel structural systems to roof the gigantic building in a world-class insulated 7 layer roofing system completed in Aluminium.
The entire roof system comprised of 7 independent insulating layers, laid layer by layer, by hand, over a coverage area of over 45 acres. That led to almost 7 x 45 = 315 acres of roofing laid in less than 12 months. In engineered terms, almost 1.3 million square meters of roofing came together using some of the most tough to handle roofing material in the world.
Interarch project management deployed over 30 roofing teams totaling over 1500 people at their peak, to roof the entire building.
With respect to the roofing aspect of the project, unlike the rest of the pre-engineered building business in the country, Interarch reached a new level of command on its position in the industry.
The entire components of the Terminal 3 “pre-engineered 7-Layer roofing system” was although designed completely in-house by Interarch under the requirements of the customer and their architects, however, none of the bulk material in the roofing system were produced by Interarch.
Interarch here achieved a further new dominant role by becoming one of the largest pre-engineered companies to become buyers of such large volumes of roofing material under a single contract ever in India. Interarch became the first pre-engineered steel construction solution company of its kind to source the best material from all over the world and be in a strong enough financial position to procure close to Rs 180 crore of material before the project even commenced.
Interarch designed and built for IGI T3, a roofing system to cater to a STC – 51 criteria for sound transmission, a never before achieved feat in any Indian airport, as well as insulating properties of U<0.26 W/m2
Each of the 7 layers of the 1.2million square meters of roofing was purchased by Interarch from the leading material vendors in the world and the completely imported aluminium skin was imported from Kalzip.
The ability of Interarch to complete the project under the strict safety and quality guidelines, ensured Interarch would deploy almost 50 dedicated safety and almost 50 other dedicated quality engineers on the site to ensure the highest standards of HSE regulations and quality controlled execution.
Interarch faced great unexpected challenges in the project that may have had consequences to the timelines and safety of the project and worked in all aspects and under all weather conditions to deliver a completely dry and world class roofing system.
After the completion of the DIAL IGI Terminal 3 project, Interarch can safely position itself to be the largest turnkey pre-engineered steel construction solution provider to have successfully moved from being just a pre-engineered building company to one of the only EPC Pre-Engineered Steel Construction Solution Providing giants in India.
Interarch today stands strong and capable of handling any infrastructure and mission critical project and delivering the entire building in steel.
Interarch’s and Tata Motors association dates back to the 1990’s, when Interarch started working with the company for roofing projects for their Pune facilities.Since then, over the last two decades, Interach has been actively involved in completion of pre-engineered structures for five manufacturing units for Tata Motors across various locations in the country.
Tata Motors, understanding their limitations to provide high quality personal vehicles from their Pune truck manufacturing units, took their passenger car dreams to Uttarakhand in early 2004 with a mega land acquisition and plans to build the largest greenfield automotive project in the history of the company and India. Interarch won the bid and turnkey contract to execute the greenfield pre-engineered building project for the Uttarakhan project.
Interarch collaborated with TATA Motors and with the help of their vetran in-house planning designed concepts for a completely new manufacturing facility that would cover almost 250,000 sq meters of production space were made ready. All buildings had to be designed from scratch keeping in mind the stringent reqiurements and time limitations of the manufacturer.
Construction work on their first manufacturing facility in was started in early 2006 in Pantnagar. This facility would cater to the production of their new innovative ‘Tata Ace’ truck utility vehicle platform. The timeline for the plant required them to be up and running in under 12 months, for first production of the new Ace Truck.
Interarch started work with TATA motors at Pantnagar, and set up the entire facility in under 10 months that was fit out in time and the first test cars rolled out in 12 months as planned.
For any automotive manufacturing facility – right from the point you break ground for construction, the clock starts ticking for the time one can start production and hence make the unit economically viable. Interarch’s PEB solutions are the most suited and proven structures to be able to meet these tight deadlines without compromising on quality.
Interarch’s manufacturing facility at Pantnagar took the challenge of manufacturing the complete plant for Tata Motors given all the above constraints. A total of 10 engineers,15 supervisors along with 800 workers were on the job over the period to ensure that quality was not compromised and roll out at the earliest The project which was erected in record time, was handed over to begin operations in 2 months post completion with a total of 16000 MT of steel supplied and erected and 354000 Sq. M of roof supplied and installed at the Pantnagar facility.
The Paint shop at the facility which also is the largest paint shop in Asia is 250 m long and has a height of 25 metres.
To save time, Interarch manufactured all the building sections in-house in the Pantnagar factory and transported them to the construction site overnight in separate lots. Close to over 300,000 parts and sections were transported to site along with hardware for assembly during the course of the project execution.
Once the material reached the site, each part and piece for the massive structure of the manufacturing facility was put in line under a project manager along with 10 engineers and 15 supervisors. The key highlights for the structure involved the creation of a mezzanine with two floors along with the conveyor corridor that connected the assembly shop to the paint shop and the engine shop. All site coordination was done by Interarch from its Central Control at the location.
The State-of-the-art facilities include weld shops, paint shops, engine and gear box shops and assembly lines. TATA Motors has invested close to Rs.1000 crores in the plant. Vendors for the vehicle have made additional investments to set up their plants in the vendor park adjoining the plant. The operation has generated about 7500 direct and indirect jobs in the plant, among vendors and service providers in the area.
This project reflects Interarch’s ability to execute turn-key solutions from design, manufacture, supply, logistics and project handling.
The ability of Interarch to complete the project under the strict safety and quality guidelines, ensured completion of the project within stipulated time even after facing many challenging situations.
Interarch today stands strong and capable of handling any infrastructure and mission critical project delivering the highest levels of quality and innovation.
The much spoken about Singur plant of Tata motors from where the Tata Nano was to be manufactured, was erected in a record time of 6 months and further finishing took 3 months despite the fact that Interarch faced problems like loose soil and flooding of the entire paint shop and engine shop.
However, unfortunately, with all the problems that engulfed the Singur plants operation, Interarch also played a key role in further expansion of the Pant Nagar plant in Uttarakhand which eventually became the location for rolling out the Tata Nano and Tata Ace.
After the Singur plant was stalled, it became pertinent for Tata to increase the capacity of the Pantnagar plant in the least possible time, as the roll out plan for the Nano had to begin.
Interarch has since then built further expansion phases at the Pantnagar facility to cater to the increasing capacity demands at the production factility.
Interarch has also executed many manufacturing plants for machine tools and heavy automotive for TATA group comanpanies.
The Tal Manufacturing Solution Ltd plant in Nagpur, a sister company of TATA, was built by Interarch. Further, Interarch has also executed the manufacturing plant for Marcopolo buses in Dharwad, a manufacturing facility for earth moving and mining equipment for Telco Construction Equipment Company,Tata Motors Facilities in Bangalore and Lucknow, and facilities for the TATA vendor parks - Ancillary units that feed and support all the manufacturing facilities.
The Paint Industry has been growing at a healthy rate over the past few years , Asian Paints is the market leader in decorative paints both distemper as well as emulsion paints. The company has a market share of over 65% of the decorative paints in India. Looking at the current & future demand of the product in market Asian paint decided to construct its 8th greenfield paint manufacturing plant in India with a window of only 8-10 month, the company aims to start production from this facility by mid of this year. The turnkey contract for constructing of this plant near Pune with the initial capacity of 150,000 tonnes was awarded with a value of 40 Cr. to Interarch.
The main challenge in front of Interarch at this time was to finish the project in the stipulated time period along with high safety expectations of the client. Another challenge in front of Interarch was the extreme dimensions of the buildings required by client for manufacturing process and stacking of raw materials, the entire project has 18 buildings in totality had variable heights with buildings towering at those of up to 30 M and had clear spans of upto of 44 M. The total project consumed more than 3000 MT of steel for structural system and around 70,000 Sq. of roofing & sheeting was supplied and installed. The entire pre-engineered steel was manufactured in InterarchPant Nagar plant and to overcome the shortness of time 3 shifts with over 150 workers & supervisor’s was started for nearly 2 months. Separate bays were created in the manufacturing plant to paint the rafters and beams as desired by the client. It took over 2 months to manufacture the steel and roofing system required.
Once at site the erection process of 18 buildings was initially were hard to manage. To satisfy the client safety expectations we had to hire the entire erection team from South East Asia.
Further, to save time no scaffolding were used and only electronic boom lifts were employed with specially trained manpower. For the first time safe roof access of 35 M high was created by Interarch of Pipe Structure and for safety inspection.
Interarch played an integral role in bringing up the steel buildings of Asian Paints in a short span of time with 18 buildings in remote location near Pune. The manufacturing plant were made using Interarch’s much spoken about roofing systems TRACDEK® Standing Seam Roofing system, with cladding systems of TRACDEK® Hi-Rib SMP.
The ability of Interarch to complete the project under the strict safety and quality guidelines ensured Interarch would deploy almost 17-20dedicated safety engineers and almost 15 other dedicated quality engineers on the site to ensure the highest standards of HSE regulations and quality controlled execution
The client has also awarded Interarch Building Products for ensuring safe & healthy work environment at site.
Project Name | Asian Paints Ltd |
---|---|
Building Location | Village Khandala, Pune Satara Road, Maharashtra |
Building Usage | Greenfield expansion projects for Asian Paints |
Tonnage of building | 3,000 MT |
Roofing Supplied in MT | 70,000 Sq.M |
Value of Project | 40 Cr. |
Area of Project | 65000 Sq. M |
Important Feature of Project : |
|
The Indian Pre-Engineered Market is at a very nascent stage currently with very less penetration in few Sectors and one of them is the growing power sector of India which still employees conventional method of construction. This is also the case with Bharat Heavy Electrical Ltd which generally uses conventional method of construction for its manufacturing units across India , the need of power is growing at a very fast pace whereas the supply is still not been able to keep up. BHEL also with very stringent timeline to start a new production line for their Pipe Manufacturing plant which will be utilized in turbines contacted Interarch.
BHEL Trichy, was of high importance to them and would be major manufacturing unit of BHEL family, an ISO9001, 14001 and OHASAS 18001 company also well on its journey towards TQM. After understanding all the requirement and Interarch willingness to execute this project and past history of successfully delivering projects of major power companies like Siemens Ltd,Gujarat Industries Power Company Ltd,BOC India Limited&Crompton Greaves Ltdby Interarch,BHEL awarded the order worth 41 Cr. for design, fabrication, supply and erection of Pre-engineered steel Building for their upcoming Greenfield Project.
The site location of the manufacturing plant was so remote that it was difficult to find un-skilled labour even, with no population in nearby areas Interarch has to arrange for worker from as far as 30 Km. The deadline to complete the project was 8 months for engineering , manufacturing, logistic and complete erection of the buildings. Another major concern was the monsoons and rains. The site was completely flooded with water, due to which the ground got soft and uneven. Work started simultaneously at the site location and Interarch Design Center.
The Project Management team of Interarch shifted their mobile office to site and design engineers started working on the design of the complex building which had a main buildings measuring 230 M X 120 M , with two connecting bay to the main buildings with size 30 M X 180 M.The challenge in front of the design team was to give loading to this building in such a way that the cost quoted for the project does not increase and the connecting building could withstand the weight of 30 MT working craneswhich will be utilized in the manufacturing process. The building has many complex features like multiple EOT all over 20 MT capacities for entire building area running in tandem for multi-station function. & up to 32 m long crane beam unsupported length to meet functional need of manufacturing.
To compensate the air-changes requirements and provide healthy enviornment to the workers inside the manufactuing plant Interarch installed 900 mm throat turbo vents on the roofs for the first time.
The project management team for safety, security, quality and project execution hired around 200 semi-skilled and unskilled labors and stated work with leveling the ground, JCB were employed to finish project in schedule. Once the design was complete the entire manufacturing of 3500 MT of built up took 2 months to manufacture at Interarch pantnagar manufacturing facility as per stringent quality control and inspection provided by the client.
At site highest level of safety and installation procedure was adopted to meet BHEL international standard of working. To complete the erection process in time Interarch employed 2 shifts of workers to work day and night.
The entire erection process of the building has been done through electronically operated boom lifts instead of traditional scaffoldings to meet safety guideline.
Time was very important and with Interarch past history of delivering projects in stipulated time period, we did not take more than a fraction of second to decide to shift the manufacturing of all the roofing and sheeting which will be utilized in the project to the site with all the difficulties in logistic to the site location and security hurdles at site.
The entire manufacturing of 42,000 Sq. M of Interarch TRACDEK® Standing Seam colored roofing system with very lean slope to achieve aesthetic view of the building took place at the site.
Interarch overcome difficult situation like Monsoon, remote location, uneven & soft soils, and complex building design but delivered the project with-in stipulated time period of 8 months.
With this project delivered on time we again prove that at Interarch "We don’t just supply buildings We deliver projects"
Project Name | BHEL |
---|---|
Building Location | Trichy, Tamil Nadu |
Building Usage | Manufacturing Unit |
Tonnage of building | 3500 MT |
Roofing Supplied in MT | 42,000 Sq. M |
Value of Project | 41 Cr. |
Area of Project | 28000 Sq. M |
Manpower deployed | 200 semiskilled and unskilled |
Important Feature of Project : |
|
The versatility of pre-engineered steel buildingsand engineering is rising on the growth curve. Light Pre-engineered buildings, and heavier project work using pre-engineered building solutions have not only proved to be relevant and beneficial to all construction verticals such as Airports, infrastructure, multi-storey buildings, power plants, industrial buildings, manufacturing plants, oil & gas refineries and group housing, but, as little known, they are the most apt and efficient for warehousing, due their highly efficient form of construction.
The range of application of pre-engineered building solutions in airport cargo centers and standalone cargo hubs and distribution centers is huge. Pre-engineered solutions used in cargo and warehousing buildings offer limitless possibilities to the end user. The pre-engineered building design philosophy takes maximum advantage when used in warehousing and cargo, as due their simplistic use for cover and storage, cargo buildings are light and pre-engineered design allows the buildings to be extremely efficient and economical to building, maintain and operate. Interarch has been key in holding flag in cargo and warehousing projects, to name a few, we have constructed large logistic facilities and cargo hubs for companies like Safe Express, GATI Cargo, Hind Terminals, Pipava Port, Dharamtar Port, SurashtraContrainings and Container Coporation of India Ltd.
Going even further our cargo buildings on airside facilities at airports include Air Cargo Warehouse for Indian Airlines, Jet Airways, Spice Jet and the recently inaugurated Delhi Cargo multi-level warehouse complex IGI Airport New Delhi, that was won and completed in 2011.
The Delhi Cargo Service Centre project at IGI New Delhi is a very large cargo center, and is a one of a kind multi-level cargo facility. Find below key features of the project:
Project Name | Delhi Cargo |
---|---|
Building Location | Indra Gandhi International Airport, New Delhi |
Building Usage | Cargo Warehouse-ground + 2 multistory building |
Tonnage of building | 5068 MT |
Roofing Supplied in MT | 426,000 Sq. M |
Value of Project | 40 Cr. |
Area of Project | 25000 Sq. M |
Important Feature of Project : |
|
Interarch boast in saying that we have designed, produced, erected & delivered almost all but one TATA motors manufacturing plants in India, and that too because of the unforseen difficulties faced in Singur. Even after having a sister company in the Tata Group as our competitor, Interarch has been instrumental in providing and satisfying all the growing needs of not only TATA Motors but other major automotive players like Fiat, GM, Skoda motors, Bajaj across India as well.
For increase in production capacity of its light truck and marcopolo buses, which has strong demand in the Market Tata Motors set-up a new project in Dharwad, Karnataka. The Ace is currently manufactured at the company's Pantnagar plant in Uttarakhand, and the Dharwad plant will be the 2ndfacility for the light-truck, after the production at Pantnagar reached full capacity.
With past history of more than 2 decades and delivery of more than 5 Green field manufacturing projects and over 100 buildings for Tata motors, Interarch was the obvious choice of Tata motors for this project also. Tata motors wanted to construct this plant not only in record time to carter the growing demand of the mini truck , but also wanted the state of the art manufacturing facility to be built with Green building norms. After completion this will be the first Green "Greenfield automotive project" in the history of the company and India.
The green manufacturing facility with numerous buildings like Paint Shop with 4 bays, Engine shop, main plant building, administrative blocks etc. worth 86 Cr was awarded to Interarch. The plants once complete will be spread over an area over 72,000 Sq. M.
Interarch proposed green feature as follows for the manufacturing facility keeping IGBC norms under consideration.
The expertise of Interarch design department reduced the engineering time of the manufacturing plant which were very complex, the main building and the paints shop was designed using IS-1984 designed building structure norms with heavy collateral loading to meet all manufacturing and MEP support needs. The paint shop building was even further complex as there were Multilevel mezzanines in the building with heavy collateral load for paint equipment installations and application provided by DURR with lot of auxiliary structure to meet functional requirement.
The Monsoon season & remote location of the site with lean population in the nearby area along with high safety standard required by TATA was a very big challenge.
Interarch had to employee many innovation solutions like highest safety standard followed in line with international standard and TML guideline to achieve zero accident, Logistic and warehousing control at site to meet site standard norms, Daily tool box meeting to review the site status and way forward was done, regular Quality check jointly with client ware done & corrective action to achieve best quality in line with global standard were taken
The entire manufacturing plant consumed more than 5000 MT of steel which was supplied by Interarch manufacturing facilities in less than 4 months.
Highest level of safety standard was showcased by Interarch Project Management team at the site achieving zero accident with over 500 semi-skilled and un-skilled labours employed at the site at the peak time.
To complete the projects in time and to exceed quality norms set by the client Interarch did site roll forming for entire roofing systems, cladding systems, liner etc. This helped in conserving time and we were able to get endless length of the sheeting. The complete manufacturing plant along with the paint shop consumed more than 72,000 Sq. M of roofing and cladding
The ability of Interarch to complete the project under the strict safety and quality guidelineshas made us the market leaders in the Pre-Engineered Buildings Sector.
Project Name | TATA Motors Ltd |
---|---|
Building Location | Dharwad, Karnataka |
Building Usage | Manufacturing Facility |
No. of Buildings | 11 |
Tonnage of building | 5400 MT |
Roofing Supplied in MT | 83,000 Sq. M |
Value of Project | 86 Cr. |
Area of Project | 72,000 Sq. M |
Manpower deployed | 500 |
Important Feature of Project : |
|