Tata Motors Ltd. |
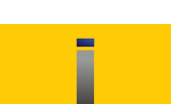 |
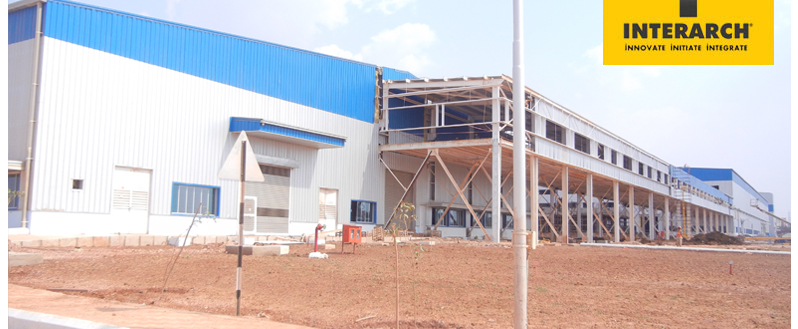 |
|
First Green Automotive Manufacturing Plant Built by Interarch in India for Tata Motors Ltd. |
|
Interarch boast in saying that we have designed, produced, erected & delivered almost all but one TATA motors manufacturing plants in India, and that too because of the unforseen difficulties faced in Singur. Even after having a sister company in the Tata Group as our competitor, Interarch has been instrumental in providing and satisfying all the growing needs of not only TATA Motors but other major automotive players like Fiat, GM, Skoda motors, Bajaj across India as well.
For increase in production capacity of its light truck and marcopolo buses, which has strong demand in the Market Tata Motors set-up a new project in Dharwad, Karnataka. The Ace is currently manufactured at the company's Pantnagar plant in Uttarakhand, and the Dharwad plant will be the 2ndfacility for the light-truck, after the production at Pantnagar reached full capacity.
With past history of more than 2 decades and delivery of more than 5 Green field manufacturing projects and over 100 buildings for Tata motors, Interarch was the obvious choice of Tata motors for this project also. Tata motors wanted to construct this plant not only in record time to carter the growing demand of the mini truck , but also wanted the state of the art manufacturing facility to be built with Green building norms. After completion this will be the first Green "Greenfield automotive project" in the history of the company and India.
The green manufacturing facility with numerous buildings like Paint Shop with 4 bays, Engine shop, main plant building, administrative blocks etc. worth 86 Cr was awarded to Interarch. The plants once complete will be spread over an area over 72,000 Sq. M.
Interarch proposed green feature as follows for the manufacturing facility keeping IGBC norms under consideration.
- Low VOC paint to be used on buildings
- All buildings to have white roof
- Special glazing for windows with sun shed to meet IGBC norms.
- Ventilation system would be designed in such Unique way that it will help in proper air flow and temperature control thus providing healthy & comfortable indoor environment.
- Bare Galvalume with sleep slope(>1:6)- this minimizes the heat island effect
- Install 3-5 % skylights on the roof of the total roof area of the building which reduces the need of artificial lights inside the building and saves electricity
The expertise of Interarch design department reduced the engineering time of the manufacturing plant which were very complex, the main building and the paints shop was designed using IS-1984 designed building structure norms with heavy collateral loading to meet all manufacturing and MEP support needs. The paint shop building was even further complex as there were Multilevel mezzanines in the building with heavy collateral load for paint equipment installations and application provided by DURR with lot of auxiliary structure to meet functional requirement.
The Monsoon season & remote location of the site with lean population in the nearby area along with high safety standard required by TATA was a very big challenge.
Interarch had to employee many innovation solutions like highest safety standard followed in line with international standard and TML guideline to achieve zero accident, Logistic and warehousing control at site to meet site standard norms, Daily tool box meeting to review the site status and way forward was done, regular Quality check jointly with client ware done & corrective action to achieve best quality in line with global standard were taken
The entire manufacturing plant consumed more than 5000 MT of steel which was supplied by Interarch manufacturing facilities in less than 4 months.
Highest level of safety standard was showcased by Interarch Project Management team at the site achieving zero accident with over 500 semi-skilled and un-skilled labours employed at the site at the peak time.
To complete the projects in time and to exceed quality norms set by the client Interarch did site roll forming for entire roofing systems, cladding systems, liner etc. This helped in conserving time and we were able to get endless length of the sheeting. The complete manufacturing plant along with the paint shop consumed more than 72,000 Sq. M of roofing and cladding
The ability of Interarch to complete the project under the strict safety and quality guidelineshas made us the market leaders in the Pre-Engineered Buildings Sector.
|
|
|
|
|
Key Project Highlight |
|
|
Project Name |
TATA Motors Ltd |
Building Location |
Dharwad, Karnataka |
Building Usage |
Manufacturing Facility |
No. of Buildings |
11 |
Tonnage of building |
5400 MT |
Value of Project |
86 Cr. |
Area of Project |
72,000 Sq. M |
Manpower deployed |
500 |
Important Feature of Project: |
 |
Complete factory will designed and manufactured under the norms of Green Buildings |
 |
Multilevel mezzanines with heavy collateral load for paint equipment installations |
 |
IS-1984 designed building structure with heavy collateral loading to meet all manufacturing and MEP support needs |
 |
Regular Quality check and action jointly with client to achieve best quality in line with global standard |
 |
Site roll forming for entire roofing , cladding, liner etc. for faster manufacturing and Quality control |
 |
Highest level of safety standard achieving zero accident with 500 semiskilled and unskilled labours at the peak time. |
|
|
|
|
|
|
|
© Copyright 2010, all rights reserved with Interarch Building Products Pvt. Ltd.
visit us at: www.interarchbuildings.com, www.interarchinfra.com |
 |
|